Conformal coatings, made with Trilene® liquid EPDM polymers, are lighter and easier to test, repair, and remove compared to many other elastomeric resins used in conformal coatings. The reversible polymer allows maintenance and repairs to expensive electronic parts instead of total discard and part replacement.
Trilene® provides better electrical properties than silicone and urethane elastomers. It offers an electric resistance of greater than 106 ohm-cm and dielectric constants of 2.2 to 2.4 volts per mil. Therefore, conformal coatings made with Trilene®, exhibit excellent insulation properties and are less susceptible to electrical breakdowns in harsh environments.
Avoidance of chemical degradation may have previously been desired in critical functioning devices like in aerospace applications. But electronics have seen various technological changes where consumer demand dictated smaller, wearable and longer lasting electronic devices. Compared to competitive conformal coating resins, EPDM allows for chemical impermeability within the PCB.
Low Moisture Permeability:
Trilene® liquid EPDM polymers are hydrophobic and ideal for waterproof coatings. They exhibit ultra-low moisture permeability up to 40 times compared to natural rubber, nitrile rubber, and silicone compounds. The low moisture absorption makes the Trilene® polymers less susceptible to electrical property losses making it ideal for high humidity environments and applications.
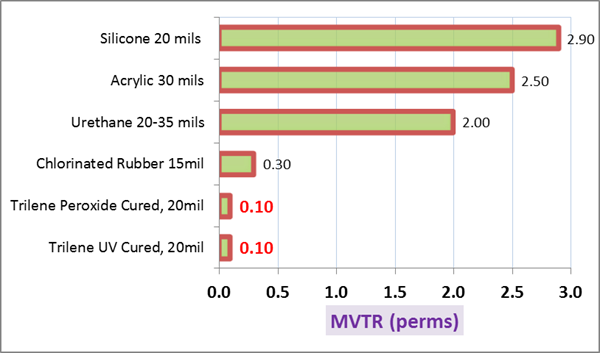
Liquid EPDM based films have very low moisture vapor transmission rates compared with other materials. MVTR is controlled through formulation where required.
Trilene® polymers offer outstanding thermal stability. It lasts about 15 times longer than either liquid polyisoprenes or polybutadienes in aging tests at 177ºC (350ºF). The liquid EPDM polymers also provide excellent adhesion to a variety of substrates and exceptional resistance to degradation by heat, light, UV, ozone, and other weathering conditions.
Trilene® polymers offer a combination of accelerated cure rate and improved aging strength not previously available with liquid hydrocarbon elastomers. Due to their low-temperature curability, Trilene® enables faster curing cycles and higher productivity. The liquid EPDM polymers can be crosslinked using peroxide, sulfur, and resin cure systems.